Choosing the wrong fluorescent sockets type—shunted or non-shunted—can lead to electrical shorts, fire hazards, and reduced lamp lifespan. Understanding their differences is crucial for safe and efficient lighting installations.
Shunted sockets have internally connected contacts, allowing current to flow through a single path; non-shunted sockets have separate contacts, providing multiple paths for current flow.
Let’s delve deeper into their distinctions and appropriate applications.
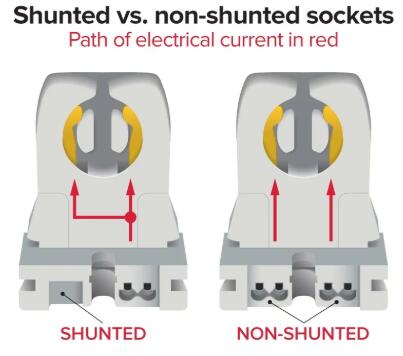
Key Differences Between Shunted and Non-Shunted Sockets
Shunted sockets have electrical contacts internally connected, which creates a single current pathway. They are commonly used with instant start ballasts, which require a high voltage to ignite lamps quickly without preheating the cathodes.
Non-shunted sockets, on the other hand, feature separate electrical contacts, providing multiple current pathways. They are compatible with rapid start and programmed start ballasts that preheat the lamp cathodes before ignition, ensuring a smoother start-up process.
How to Identify Your Socket Type
To identify whether a socket is shunted or non-shunted, use a voltage meter in continuity mode. If continuity is detected, the socket is shunted.
Visually, shunted sockets often have two wiring holes, while non-shunted sockets typically have four. However, visual inspection is not always reliable, so testing is recommended.
Applications for Shunted Sockets
Shunted sockets are ideal for instant start ballasts, which deliver high initial voltage to ignite lamps without preheating. This makes them suitable for systems where quick illumination is essential.
Additionally, plug-and-play LED tubes compatible with instant start ballasts require shunted sockets. However, using these sockets with incompatible ballasts or lamps can cause operational issues or safety hazards.
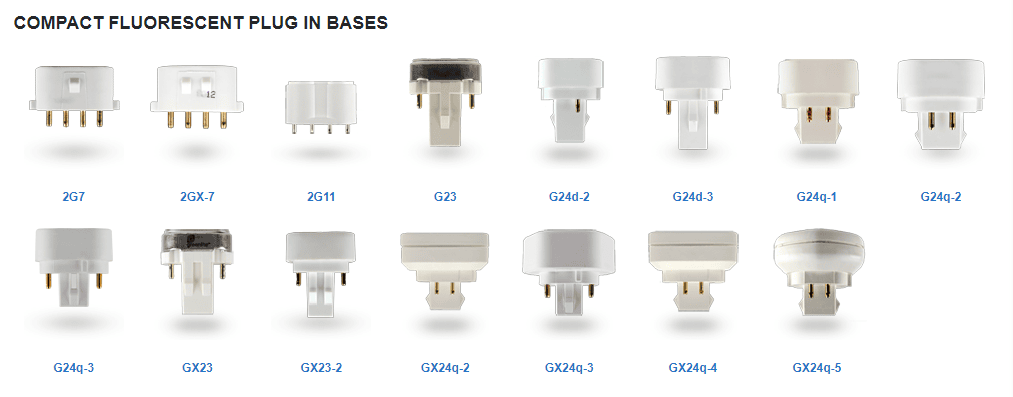
Applications for Non-Shunted Sockets
Non-shunted sockets are essential for rapid start and programmed start ballasts. These systems preheat lamp cathodes, reducing wear and extending lamp life.
Single-ended power LED tubes also require non-shunted sockets, making them indispensable in LED retrofits. Replacing shunted sockets with non-shunted ones is often necessary when converting fluorescent fixtures to LED systems.
T8 and T12 Compatibility
T8 and T12 lamps can use either shunted or non-shunted sockets, depending on the ballast type. Instant start ballasts typically require shunted sockets, while rapid start and programmed start ballasts need non-shunted sockets.
Matching the correct socket type to the ballast ensures proper operation and avoids potential safety issues.
Converting Socket Types
Converting non-shunted sockets to shunted ones is not recommended due to safety and compliance concerns. Instead, it’s safer and more reliable to replace the sockets with the correct type required for the ballast and lamp.
Replacing sockets is a straightforward process and ensures compatibility and adherence to electrical standards.
Considerations for LED Retrofits
LED retrofits require careful consideration of socket types. Plug-and-play LED tubes often need shunted sockets to work with existing ballasts, while direct wire LED tubes generally require non-shunted sockets.
Always consult the manufacturer’s guidelines when retrofitting to ensure compatibility and safety, especially when switching from fluorescent systems to LEDs.
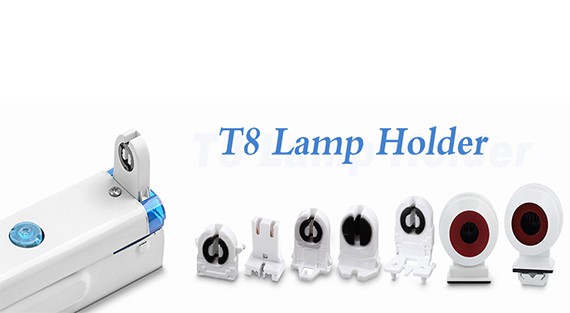
Safety Implications
Using the wrong socket type can lead to serious electrical hazards, such as shorts, fires, and equipment damage. Ensuring the compatibility of your socket, ballast, and lamp type is critical to maintaining a safe and efficient lighting system.
Identifying the correct socket type and adhering to safety standards can prevent accidents and ensure long-term system performance.
Final Words:
Understanding the differences between shunted and non-shunted sockets is essential for safe and efficient lighting installations. By matching the socket type to your ballast and lamp requirements, you can optimize performance and ensure system longevity.